PIglide RL rotation stage, air bearing, 150 mm motion platform diameter, low height, angle measuring system with sin/cos signal transmission, slotless, brushless 3-phase torque motor
A-63x PIglide RL Flat Rotation Stage with Air Bearing
Friction-free, Motorized
- 150 mm, 200 mm or 350 mm
- motion platform diameter
- Low profile
- Eccentricity and flatness < 100 nm
- Option for self-locking at rest by magnetic preload
Product overview
The directly driven low-profile rotation stages of the PIglide RL series are designed for the highest precision with low-profile design. Various options can be combined to create a solution ideal for point-to-point indexing or constant velocity scanning. The RL stages offer superior travel accuracy, flatness, and wobble performance.
3-Phase torque motor
- Brushless
- Slotless
- Low cogging torque
Absolute encoder (optional)
Absolute encoders supply explicit position information that enables immediate determination of the position. This means that referencing is not required during switch-on, which increases efficiency and safety during operation.
Accessories and options
- Incremental or absolute encoder
- Vacuum feedthrough
- Self-locking at rest by magnetic preload
- Clear aperture on request
- PIglide filter and air preparation kit
- Single or multi-axis motion controllers and servo drives
- Multi-axis/customized setups
- Base plates made of granite and systems for reducing vibration
Application fields
Optical alignment, wafer inspection, wafer alignment, measuring technology, inspection systems, calibration, scanning.
Thanks to the friction-free motion, no particles are formed, which makes PIglide stages ideal for cleanroom applications.
Specifications
Datasheet A-63x
Specifications
Motion | A-634.A100 | A-634.B100 | A-635.A100 | A-635.B100 | A-638.A100 | A-638.B100 | Tolerance |
---|---|---|---|---|---|---|---|
Active axes | θZ | θZ | θZ | θZ | θZ | θZ | |
Rotation range in θZ | 360 ° | 360 ° | 360 ° | 360 ° | 360 ° | 360 ° | |
Maximum angular velocity in θZ, unloaded | 500 rpm | 500 rpm | 500 rpm | 500 rpm | 500 rpm | 500 rpm | |
Radial error in X | ± 0.1 µm | ± 0.1 µm | ± 0.075 µm | ± 0.075 µm | ± 0.005 µm | ± 0.005 µm | max. |
Axial error | ± 0.038 µm | ± 0.038 µm | ± 0.038 µm | ± 0.038 µm | ± 0.025 µm | ± 0.025 µm | max. |
Tilt error around X (wobble) | ± 1 µrad | ± 1 µrad | ± 1 µrad | ± 1 µrad | ± 0.5 µrad | ± 0.5 µrad | max. |
Positioning | A-634.A100 | A-634.B100 | A-635.A100 | A-635.B100 | A-638.A100 | A-638.B100 | Tolerance |
Positioning accuracy in θZ, calibrated | ± 8 µrad | ± 8 µrad | ± 8 µrad | ± 8 µrad | ± 8 µrad | ± 8 µrad | typ. |
Bidirectional repeatability in θZ | 4 µrad | 4 µrad | 4 µrad | 4 µrad | 4 µrad | 4 µrad | typ. |
Reference switch | 1 / revolution, differential pulse over one sensor signal period, 1 V peak-peak | — | 1 / revolution, differential pulse over one sensor signal period, 1 V peak-peak | — | 1 / revolution, differential pulse over one sensor signal period, 1 V peak-peak | — | |
Integrated sensor | Incremental angle-measuring system | Absolute angle-measuring system | Incremental angle-measuring system | Absolute angle-measuring system | Incremental angle-measuring system | Absolute angle-measuring system | |
Sensor signal | Sin/cos, 1 V peak-peak | BiSS-C | Sin/cos, 1 V peak-peak | BiSS-C | Sin/cos, 1 V peak-peak | BiSS-C | |
Sensor signal periods / U | 23600 | — | 31488 | — | 31488 | — | |
Sensor resolution, rotational | 0.06 µrad | 0.0015 µrad | 0.05 µrad | 0.0015 µrad | 0.05 µrad | 0.0015 µrad | |
Drive Properties | A-634.A100 | A-634.B100 | A-635.A100 | A-635.B100 | A-638.A100 | A-638.B100 | Tolerance |
Drive type | Ironless 3-phase torque motor | Ironless 3-phase torque motor | Ironless 3-phase torque motor | Ironless 3-phase torque motor | Ironless 3-phase torque motor | Ironless 3-phase torque motor | |
Nominal voltage | 48 V | 48 V | 48 V | 48 V | 48 V | 48 V | |
Peak voltage | 80 V | 80 V | 80 V | 80 V | 80 V | 80 V | |
Nominal current, RMS | 2.3 A | 2.3 A | 4.5 A | 4.5 A | 4.5 A | 4.5 A | typ. |
Peak current, RMS | 6.9 A | 6.9 A | 13.9 A | 13.9 A | 13.9 A | 13.9 A | typ. |
Drive torque clockwise in θZ | 1.6 N·m | 1.6 N·m | 2.8 N·m | 2.8 N·m | 2.8 N·m | 2.8 N·m | max. |
Drive torque counterclockwise in θZ | 1.6 N·m | 1.6 N·m | 2.8 N·m | 2.8 N·m | 2.8 N·m | 2.8 N·m | max. |
Peak torque clockwise in θZ | 4.7 N·m | 4.7 N·m | 8.5 N·m | 8.5 N·m | 8.5 N·m | 8.5 N·m | max. |
Peak torque counterclockwise in θZ | 4.7 N·m | 4.7 N·m | 8.5 N·m | 8.5 N·m | 8.5 N·m | 8.5 N·m | max. |
Torque constant | 0.59 N·m/A | 0.59 N·m/A | 0.66 N·m/A | 0.66 N·m/A | 0.66 N·m/A | 0.66 N·m/A | typ. |
Resistance phase-phase | 6.7 Ω | 6.7 Ω | 4.5 Ω | 4.5 Ω | 4.5 Ω | 4.5 Ω | typ. |
Inductance phase-phase | 0.9 mH | 0.9 mH | 0.6 mH | 0.6 mH | 0.6 mH | 0.6 mH | |
Back EMF, phase-phase, rotational | 71 V/kRPM | 71 V/kRPM | 80 V/kRPM | 80 V/kRPM | 80 V/kRPM | 80 V/kRPM | max. |
Mechanical Properties | A-634.A100 | A-634.B100 | A-635.A100 | A-635.B100 | A-638.A100 | A-638.B100 | Tolerance |
Permissible push force in X | 40 N | 40 N | 80 N | 80 N | 200 N | 200 N | max. |
Permissible push force in Y | 40 N | 40 N | 80 N | 80 N | 200 N | 200 N | max. |
Permissible push force in Z | 190 N | 190 N | 320 N | 320 N | 1200 N | 1200 N | max. |
Permissible torque in θX | 4.5 N·m | 4.5 N·m | 12 N·m | 12 N·m | 130 N·m | 130 N·m | max. |
Permissible torque in θY | 4.5 N·m | 4.5 N·m | 12 N·m | 12 N·m | 130 N·m | 130 N·m | max. |
Moment of inertia in θZ, unloaded | 6710 kg·mm² | 6710 kg·mm² | 21580 kg·mm² | 21580 kg·mm² | 147090 kg·mm² | 147090 kg·mm² | ±20 % |
Moved mass in θZ, unloaded | 1900 g | 1900 g | 3600 g | 3600 g | 11000 g | 11000 g | ±5 % |
Bearing type | Air bearings with magnetic preload | Air bearings with magnetic preload | Air bearings with magnetic preload | Air bearings with magnetic preload | Air bearings with magnetic preload | Air bearings with magnetic preload | |
Overall mass | 4600 g | 4600 g | 7500 g | 7500 g | 24000 g | 24000 g | ±5 % |
Material | Hardcoat aluminum, stainless steel mounting hardware | Hardcoat aluminum, stainless steel mounting hardware | Hardcoat aluminum, stainless steel mounting hardware | Hardcoat aluminum, stainless steel mounting hardware | Hardcoat aluminum, stainless steel mounting hardware | Hardcoat aluminum, stainless steel mounting hardware | |
Miscellaneous | A-634.A100 | A-634.B100 | A-635.A100 | A-635.B100 | A-638.A100 | A-638.B100 | Tolerance |
Operating temperature range | 15 to 25 °C | 15 to 25 °C | 15 to 25 °C | 15 to 25 °C | 15 to 25 °C | 15 to 25 °C | |
Connector | D-sub 9W4 (m) | D-sub 9W4 (m) | D-sub 9W4 (m) | D-sub 9W4 (m) | D-sub 9W4 (m) | D-sub 9W4 (m) | |
Sensor connector | D-sub 15 (m) | D-sub 15 (m) | D-sub 15 (m) | D-sub 15 (m) | D-sub 15 (m) | D-sub 15 (m) | |
Operating pressure | 515 to 585 kPa | 515 to 585 kPa | 515 to 585 kPa | 515 to 585 kPa | 515 to 585 kPa | 515 to 585 kPa | |
Air consumption | 56 L/min | 56 L/min | 56 L/min | 56 L/min | 56 L/min | 56 L/min | max. |
Air quality | Clean (filtered up to 1.0 µm or better) - ISO 8573–1 class 1 ǀ Oil free - ISO 8573–1 class 1 ǀ Dry (-15 °C dew point) - ISO 8573–1 class 3 | Clean (filtered up to 1.0 µm or better) - ISO 8573–1 class 1 ǀ Oil free - ISO 8573–1 class 1 ǀ Dry (-15 °C dew point) - ISO 8573–1 class 3 | Clean (filtered up to 1.0 µm or better) - ISO 8573–1 class 1 ǀ Oil free - ISO 8573–1 class 1 ǀ Dry (-15 °C dew point) - ISO 8573–1 class 3 | Clean (filtered up to 1.0 µm or better) - ISO 8573–1 class 1 ǀ Oil free - ISO 8573–1 class 1 ǀ Dry (-15 °C dew point) - ISO 8573–1 class 3 | Clean (filtered up to 1.0 µm or better) - ISO 8573–1 class 1 ǀ Oil free - ISO 8573–1 class 1 ǀ Dry (-15 °C dew point) - ISO 8573–1 class 3 | Clean (filtered up to 1.0 µm or better) - ISO 8573–1 class 1 ǀ Oil free - ISO 8573–1 class 1 ǀ Dry (-15 °C dew point) - ISO 8573–1 class 3 | |
Recommended controllers / drivers | A-81x (1, 2, or 4 axes) A-82x (4, 6, or 8 axes) | A-81x (1, 2, or 4 axes) A-82x (4, 6, or 8 axes) | A-81x (1, 2, or 4 axes) A-82x (4, 6, or 8 axes) | A-81x (1, 2, or 4 axes) A-82x (4, 6, or 8 axes) | A-81x (1, 2, or 4 axes) A-82x (4, 6, or 8 axes) | A-81x (1, 2, or 4 axes) A-82x (4, 6, or 8 axes) |
Note on linear and rotational crosstalk: Dependent on the quality of the underlying surface, the payload, orientation, and forces that act on the stage from the outside. Please contact PI for
application-specific parameters. The specified values are static (no rotary motion during measuring) and without load.
Note on permissible push force and permissible torque: The values listed assume a supply pressure of 550 kPa (80 psi). Please contact PI if other pressures are required.
Note on angular velocity: May be limited by the payload, payload imbalance, controller or drive.
Note on sensor resolution for A-63x.A100: Assumes 4096x interpolation. Contact PI for the use of other factors.
Note on positioning accuracy: The specified values are based on error compensation controlled by the controller. The stage must be ordered with an A-8xx series controller from PI to reach these values. Accuracy values assume short-term duration and do not consider the long-term effects of thermal drift on the stage.
Note on operating pressure: To protect the stage against damage, it is recommended to connect an air pressure sensor to the Motion-Stop input of the controller.
Ask about customized versions.
At PI, technical data is specified at 22 ±3 °C. Unless otherwise stated, the values are for unloaded conditions. Some properties are interdependent. The designation "typ." indicates a statistical average for a property; it does not indicate a guaranteed value for every product supplied. During the final inspection of a product, only selected properties are analyzed, not all. Please note that some product characteristics may deteriorate with increasing operating time.
Downloads
Datasheet
Datasheet A-63x
Documentation
User Manual A630D0001
A-63x Series Low Profile Rotary Air Bearing Stage PIglide RL, Direct-drive Torque Motor Driven with Encoder Feedback
3D Models
A-63x 3-D model
Ask for a free quote on quantities required, prices, and lead times or describe your desired modification.
PIglide RL rotation stage, air bearing, 150 mm motion platform diameter, low height, absolute angle-measuring system with BiSS-C signal transmission, slotless, brushless 3-phase torque motor
PIglide RL rotation stage, air bearing, 200 mm motion platform diameter, low height, angle measuring system with sin/cos signal transmission, slotless, brushless 3-phase torque motor
PIglide RL rotation stage, air bearing, 200 mm motion platform diameter, low height, absolute angle-measuring system with BiSS-C signal transmission, slotless, brushless 3-phase torque motor
PIglide RL rotation stage, air bearing, 350 mm motion platform diameter, low height, angle measuring system with sin/cos signal transmission, slotless, brushless 3-phase torque motor
PIglide RL rotation stage, air bearing, 350 mm motion platform diameter, low height, absolute angle-measuring system with BiSS-C signal transmission, slotless, brushless 3-phase torque motor
Comment obtenir une offre de prix
Contactez un ingénieur!
Quickly receive an answer to your question by email or phone from a local PI sales engineer.
Technologie
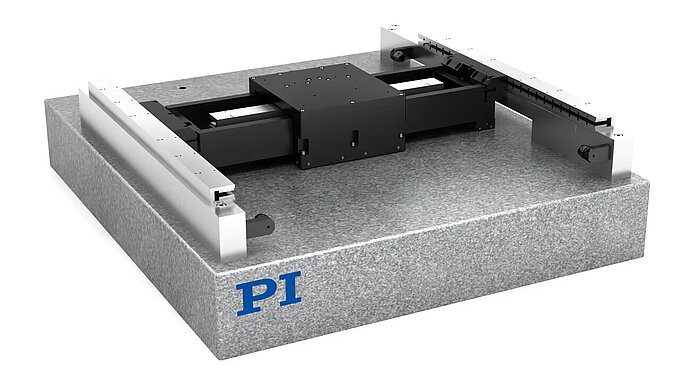
Technologie de guidage à coussin d’air PIglide
Multi-axis motion with nanometer precision and without friction.
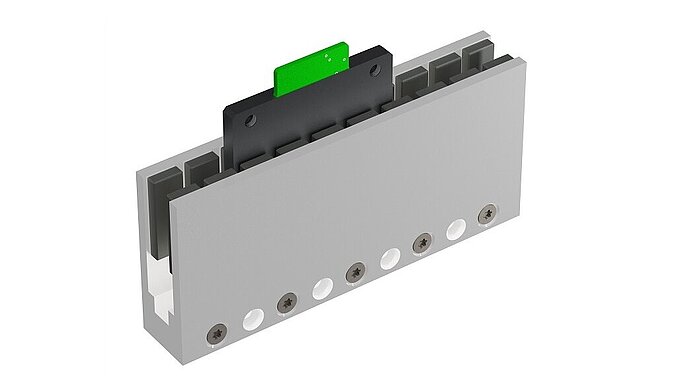
Entraînements directs magnétiques
Les entraînements directs magnétiques présentent des avantages par rapport aux technologies classiques basées sur des vis précontraintes ou à billes, notamment en termes d'usure et de dynamique.