Why PI Uses EtherCAT to Connect
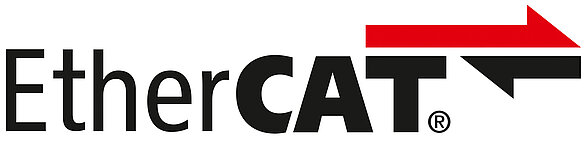
EtherCAT (Ethernet for Control Automation Technology) is an Open Real Time Ethernet-based fieldbus system.
The goal during development of EtherCAT was to apply Ethernet for automation applications requiring short data update times (also called cycle times; ≤ 100 µs) with low communication jitter (for precise synchronization purposes; ≤ 1 µs) and reduced hardware costs.
EtherCAT is becoming increasingly popular for control and system engineers as a robust, high-speed real-time network for machine control solutions. With deterministic and high speed update rates and extremely precise synchronization of all network devices, machine builders and system integrators can take advantage of dedicated motion and machine controller platforms utilizing EtherCAT to easily construct a full machine control solution while still maintaining the highest level of performance and a low cost structure.
Why use EtherCAT?
The unique way that EtherCAT works makes it the clear “engineer’s choice.” Additionally, the following features are particularly advantageous for many applications.
EtherCAT is by and large the fastest industrial Ethernet technology, but it also synchronizes with nanosecond accuracy. This is a huge benefit for all applications in which the target system is controlled or measured via the bus system. The rapid reaction times work to reduce the wait times during the transitions between process steps, which significantly improves application efficiency.
In EtherCAT applications, the machine structure determines the network topology, not the other way around. In conventional Industrial Ethernet systems, there are limitations on how many switches and hubs can be cascaded therefore limiting the overall network topology. Since EtherCAT doesn’t need hubs or switches, there are no such limitations. In short, EtherCAT is virtually limitless when it comes to network topology. Line, tree, star topologies and any combinations thereof are possible with a nearly unlimited number of nodes.
EtherCAT delivers the features of industrial Ethernet at a price similar or even below that of a classic fieldbus system. The only hardware required by the master device is an Ethernet port – no expensive interface cards or co-processors are necessary. Since EtherCAT doesn’t require switches or other active infrastructure components, the costs for these components and their installation, configuration, and maintenance are also eliminated.
Hexapod Motion Controller with EtherCAT
- Ability to control a 6-axis positioning system via EtherCAT, for example a hexapod
- Performs coordinate transformation for parallel kinematics
- Position input via Cartesian coordinates, coordinate transformation handled by the controller
- Reference system (Work, Tool) can be quickly and easily changed
- Stable, virtual pivot point can be freely defined in space
- Supports motor brakes and absolute-measuring sensors with BiSS interface
Downloads
Controlling Hexapods via EtherCAT®
Easy Integration of Six-Axis Robots into the Process Environment
Digital Multi-Channel Controller for Piezo Nanopositioning Systems with EtherCAT Fieldbus Interface
Controller and nanopositioning system behave like an intelligent multi-axis drive according to CiA402 drive profile. Can be integrated seamlessly into automation systems in industry and research. Operating modes according to IEC 61800-7-201: Cyclic Synchronous Position (CSP), Profile Position (PP) and Homing (manufacturer-specific method: Autozero). Cycle time 2 ms.
ACS Motion Controllers for Industrial Applications
- Powerful motion control solutions for demanding multi-axis automation
- Can be run as the EtherCAT Master
- Can be run as 2nd EtherCAT Master Motion Controller to be integrated in an existing PLC architecture. This allows the demanding motion to be directly controlled by the ACS within the original EtherCAT network
- Unique control algorithms, such as ServoBoost, optimize step-and-settle times
- Profile shaping prevents the excitation of vibrations
- Proprietary and patented features such as NanoPWM achieve a dynamic range of current control of higher than 100,000:1 and as a result allow a nanometer level of tracking errors and a standstill jitter in the subnanometer range
- Extensive trigger functionality, e.g., for laser applications or inspection functions
- Integrated 3 degrees of freedom compensation of positioning errors and yaw compensation for gantry solutions