F-712.Hxx Compact, High-Speed 6-DOF Photonics Alignment Systems
Single-Sided and Double-Sided, Upright and Low-Profile, Fully Automated Array Alignment Routines
- Integrated scan/align routines for SiPh wafers, photonic devices, PICs, and fiber optics
- Powerful array alignment algorithms
- Fast, simultaneous optimization across multiple devices, I/Os, and degrees of freedom (DoF)
- Broad and deep software support for rapid process development, including support for popular languages such as C#, Python, LabVIEW, and MATLAB on Windows and Linux
- Automatic alignment in typically < 0.5 s
- Responsive application and product support from PI worldwide







Problem solved
PI's Fast Multi-Channel Photonics Alignment (FMPA) solutions combine application-optimized, fab-ready, highly dynamic alignment stages with sophisticated controllers that integrate the world's most advanced and effective first-light search, profile, and power optimization alignment algorithms.
Reduction of alignment time by 99 %
This award-winning technology addresses the number one cost driver for photonics test and assembly: the precise alignment required for each element and channel. Legacy alignment technologies date back to the 1980s and can take minutes to complete. PI's fast optical alignment solutions reduce the time required by typically 99 %, routinely completing the task in less than one second. With studies indicating that on the order of 80 % of the cost of a photonic device is consumed in the alignment prior to FMPA, it is easy to see how profound the production economics benefit from reducing that 80 % by 99 %. And with projections of three orders of magnitude escalation in demand for photonic components in the near future, as new applications and devices emerge, FMPA is a true enabler.
Versatile, compact, proven solutions for 6-DoF alignment challenges
These integrated solutions combine PI's premier compact hexapod with a highly dynamic, ultra-resolution NanoCube® fast piezo scanning stage to provide 6-DoF positioning, scanning, and optimization. Since their introduction in 2016, these unique microrobotic solutions have enabled a variety of applications ranging from silicon photonics wafer probing to array alignment and automated photonics device assembly and are the first choice of many elite OEMs and in-house integration teams. The applications are complex, but the reasons for the choice are simple: groundbreaking alignment speed that improves production throughput by two orders of magnitude, an easy-to-master command set complemented by broad and deep software support, and global application expertise and support.
Synergies for higher performance
The combined hexapod and NanoCube® mechanisms operate synergistically to enable simultaneous optimization across multiple channels, I/Os, and DoF, with parallel optimization across all DoF and I/Os. For example, the NanoCube® offers extreme speed and long life through flexure guides and PICMA piezo drives, while the hexapod offers generous travel that includes pitch-yaw-roll positioning and alignment optimization important for arrayed waveguides, etc. High-resolution analog inputs provide connectivity to power measurement devices, such as PI’s F-712.PM1 high-bandwidth optical power meter, for optimization and profiling, enabling efficient and fast automated fiber optical alignment. Soft limits are supported to ensure process safety.
Low profile and upright configurations
PI’s 6-DOF fiber alignment systems include the F-712.HA1, F-712.HA2, and F-712.HU1 standard configurations.
The F-712.HA1 and F-712.HA2 single-sided and double-sided angled configurations offer a low profile. This means that the alignment can be performed close to (or even under) the mounting surface thanks to the hexapod’s angled mounting. Ideal for silicon photonics wafer probing applications.
The F-712.HU1 single-sided upright configuration is ideal for device characterization and packaging processes. Upright configurations for two or even more sides are available on request.
Starting with these sophisticated platforms, it is easy to configure further alignment solutions of unprecedented speed that support functionalities such as submicron-sensitive wafer proximity automation.
Application fields
PIC production, alignment of fiber arrays, collimators, optical components or lenses, silicon photonics wafer probing, testing, assembly, and packaging of photonics and fiber optics
Specifications
Datasheet F-712.Hxx
Specifications
Motion and positioning | F-712.HA1 | F-712.HA2 | F-712.HU1 | Unit |
---|---|---|---|---|
Number of active axes | 9 | 18 | 9 | |
Rough positioning | ||||
Active axes | X, Y, Z, θX, θY, θZ | |||
Travel range in X, Y, Z | ±6,5, ±16, ±8,5 | ±17, ±16, ±6,5 | mm | |
Travel range in θX, θY, θZ | ±14,5, ±10, ±10 | ±10, ±10, ±21 | ° | |
Minimum incremental motion in X, Y | 0.1 | µm | ||
Minimum incremental motion in Z | 0.1 | 0.05 | ||
Max. velocity | 10 | mm/s | ||
Sensor type | Incremental rotary encoder | |||
Drive type | Brushless DC motor | |||
Fine positioning | ||||
Active axes | X, Y, Z | |||
Travel range in X, Y, Z, closed loop | 100 | µm | ||
Min. incremental motion, open-loop | 0.3 | nm | ||
Min. incremental motion, closed-loop | 2.5 | nm | ||
Linearity error, for the entire travel range* | 2 | % | ||
Repeatability (bidirectional) 10% travel range | 2 | nm | ||
Sensor type | Incremental linear encoder | |||
Drive type | PICMA® | |||
Alignment | ||||
Scanning time of spiraled area scan 500 µm Ø** | < 2 | < 5 | < 2 | s |
Scanning time of spiraled area scan 100 µm Ø** | < 0.3 | < 1 | < 0.3 | s |
Scanning time of spiraled area scan 10 µm Ø** | < 0.2 | < 0.5 | < 0.2 | s |
Signal optimization with gradient search, randomized with ±5 µm (repeatability < 0.01 dB)*** | < 0.3 | s |
The maximum travel ranges of the individual coordinates (X, Y, Z, θX, θY, θZ) are interdependent. The data for each axis shows its maximum travel range when all other axes are in the zero position of the nominal travel range and the default coordinate system is in use, or rather when the pivot point is set to 0,0,0.
Downloads
Product Note
Product Change Notification Motor Driven Products
Product Change Notification Piezo Actuator Driven Products
Product Change Notification F-712.xxx
Datasheet
Datasheet F-712.Hxx
Documentation
User Manual F712T0024
F-712.HP1 Mounting Adapter for F-712.HA1 / F-712.HA2 Fiber Alignment Systems
User Manual F603T0003
F-603.41 / F-603.42 / F-603.43 Fiber holders for P-616-type (NanoCube®) piezo positioners
User Manual F712T0003
F-712.HA1 and F-712.HA2 Systems with 6 Degrees of Freedom for Fast Multi-Channel Photonics Alignment. Hardware description.
User Manual E712T0016
Fast Multi-Channel Photonics Alignment of Silicon Photonics Components with F-712 Alignment Systems and Hexapods from PI. PILightning Option for First Light Search
User Manual F712T0019
Calculation of Optical Power - Using the F-712.PM1 Power Meter with F-712 High-Precision Fiber Alignment Systems
User Manual F712T0007
F-712.HU1 High-Precision Fiber Alignment System
3D Models
F-712.Hxx 3D Model
F-712.Hxx 3D model
Livre Blanc
Case Study: Photonic Array Device Assembly
Practical Examples of Parallel Alignment Automation
Quote / Order
Ask for a free quote on quantities required, prices, and lead times or describe your desired modification.
Comment obtenir une offre de prix
Contactez un ingénieur!
Quickly receive an answer to your question by email or phone from a local PI sales engineer.
Technologie
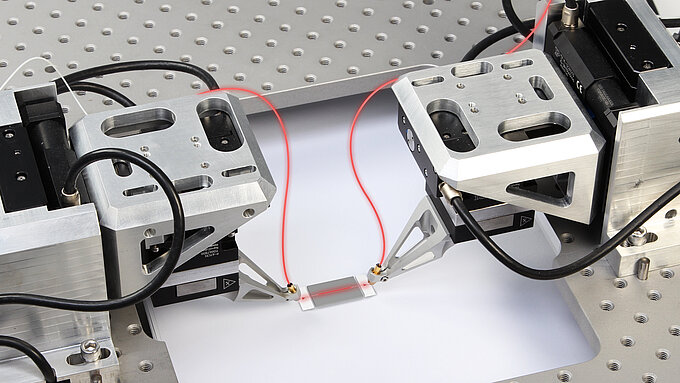
Alignement actif
The need to align devices down to nanoscale accuracy is arising in many fields. Optical components such as the lenses or lens assemblies in small cameras, or even the CCD chip itself, need to be positioned with ever more precision.
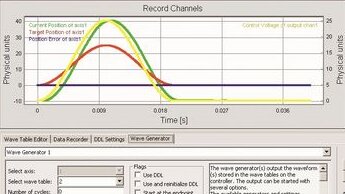
Contrôleurs numériques
Digital technology opens up possibilities for improving performance in control engineering which do not exist with conventional analog technology.
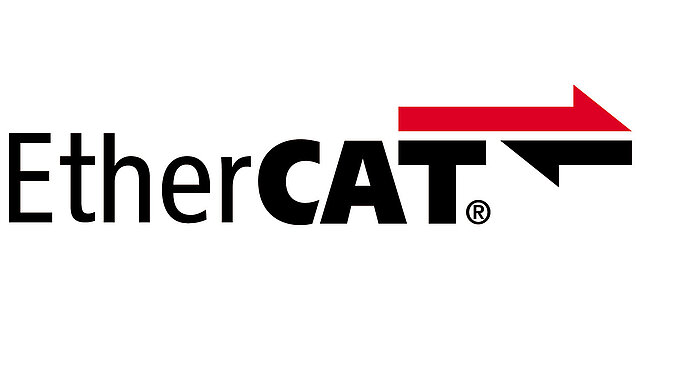
Connectivité EtherCAT des produits PI
PI offers high-precision drives for use as EtherCAT slave, or integrates with ACS Motion Controllers as Master, or 2nd Master in an existing architecture.
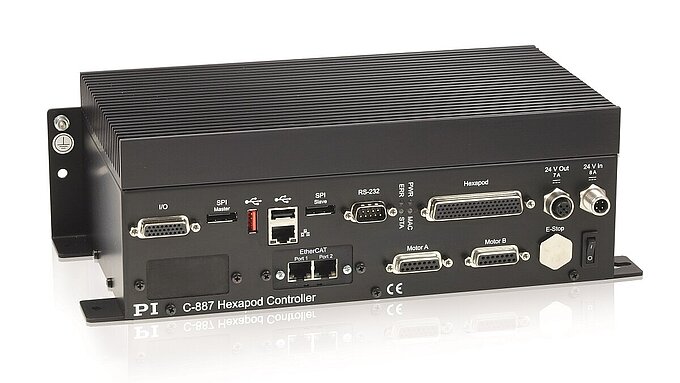
Interfaces numériques et analogiques
Fast USB or TCP/IP interfaces as well as RS-232 are the standard interfaces supported by modern digital controllers from PI. Furthermore, PI also provides digital or analog real-time capable interfaces.
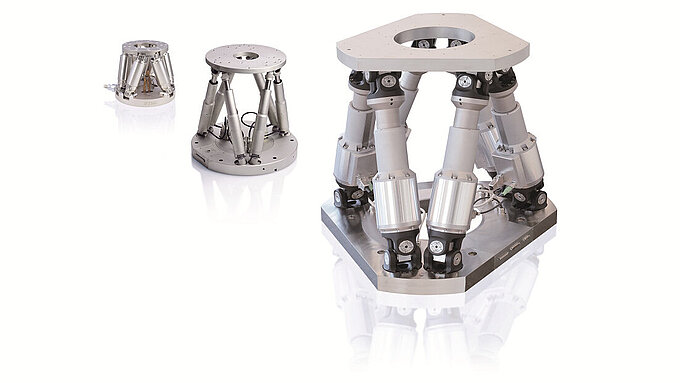
Positionneurs multiaxes
Les plateformes hexapode sont utilisées pour le positionnement de précision et l'alignement de charges selon six degrés de liberté, trois axes linéaires et trois axes rotatifs.