- Technology - Physik Instrumente (PI) GmbH & Co. KG
ILA Berlin 2024: Physik Instrumente (PI) Develops Highly Dynamic Compensation Kinematics for Aircraft Construction
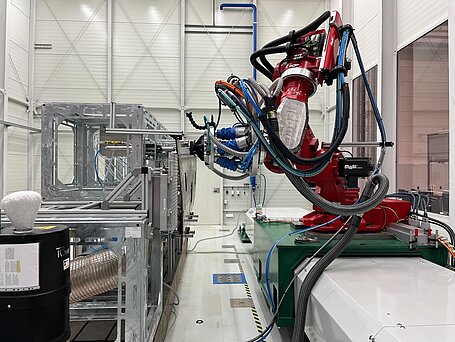
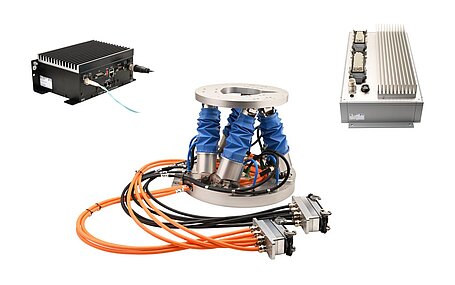
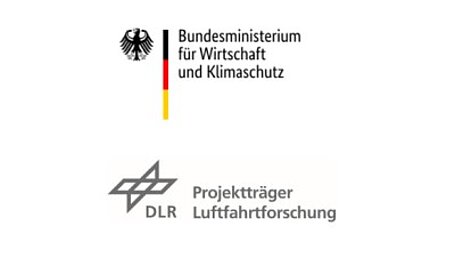
As part of the joint project, PI developed the high-performance hexapod H-900K101 for highly dynamic compensation kinematics in aircraft construction. The aim was to increase the processing and sealing precision for CFK components in RTM (resin transfer molding) manufacturing processes and to reduce manufacturing times and process costs. Thanks to its low weight and high stiffness, the fiber composite material CFK makes a decisive contribution to greater energy efficiency and CO2 savings in aircraft.
Dynamic Compensation of Process Forces
The focus of the compensation kinematics is the contour machining of the single-aisle wing shells of the Wing of Tomorrow made of CFK by means of milling and deburring, as well as their subsequent sealing and drilling. Combined with an articulated robot for rough positioning, PI's hexapod is used for the fine positioning of the machining and sealing tools. “With the new H-900K101 hexapod, we have implemented a highly dynamic system that can accelerate a payload of up to 40 kg in the XY plane at up to 12,000 mm/s². The system is able to dynamically compensate for high-frequency path deviations under the influence of process forces during milling,” explains Dr. Christian Sander, Head of Technology Development Parallel Kinematics at PI in Karlsruhe, Germany. The newly developed hexapod system was designed for the specific boundary and environmental conditions of the application and is therefore optimized in particular for the time-critical manufacturing processes with the specified tolerances of the aerospace industry.
Fine Positioning of Tools
In addition to this high dynamic performance, the hexapod system offers fiber optic data transmission between the hexapod controller and the driver electronics, a very low latency time when using the EtherCAT® interface and IP54-sealed components. Fiber optic data transmission allows the hexapod controller to be conveniently located in the control cabinet outside the processing cell without compromising the variety of interfaces while controlling the driver electronics over a distance of up to 100 m. For the EtherCAT® interface, a deep integration of the EtherCAT® functionality into PI's controller and driver architecture has been realized. As a result, PI's positioning system contributes only a minimal amount of dead time to the complex control loop for path error compensation between the edge-detection sensor system, the articulated robot, and the hexapod. The response time in the EtherCAT® control loop between the hexapod's position request and position response is 1.5 ms.
Recently, the ADMAS LuFo project investigated the use of acceleration sensors for wear detection on individual hexapod struts in the context of condition monitoring. The frequency spectrum of vibrations within a single strut can be mapped to characteristic eigenfrequencies of drive components, providing an indicator of system changes.
Modular Systems
Hexapods offer six degrees of freedom in the smallest space. For industrial applications, combinations of absolute position sensors, software, and motion controllers are available to control complex motion profiles. All drive technologies are customizable.
PI's precision hexapods are available in standard configurations for loads from 1 kg to 250 kg and repeatability to ±0.06 µm. Customized precision hexapods can support loads in excess of 2,000 kg. With travel ranges from a few millimeters to several hundred millimeters, the machines enable precision down to the nanometer range and velocities from 0.1 mm/s to 500 mm/s. PI hexapods are used worldwide in silicon photonics, automation, medical technology, astronomy, and research. Depending on requirements, they can be specified for environments such as IP54, laboratory, cleanroom, high vacuum, and ultrahigh vacuum.
About Physik Instrumente (PI) GmbH & Co. KG
PI with headquarters in Karlsruhe, Germany, is the market and technology leader for high-precision positioning technology and piezo applications in the market segments of Industrial Automation, Photonics, Semiconductor, and Microscopy & Life Sciences. In close cooperation with customers from all over the world, PI's more than 1,500 specialists have been continuously pushing the boundaries of what is technically feasible for more than fifty years. Various drive technologies, internally developed sensor technology, electronics, and control technology provide the basis for this. PI’s portfolio ranges from components to subsystems, to tailor-made complete solutions. 508 granted and pending patents underline the company's claim to leadership in the fields of precision positioning and piezo technology. PI operates on a global scale, with nine production sites in Europe, North America, and Asia, as well as sixteen sales and service subsidiaries.